Introduction
This is a common question among manufacturers seeking to optimize their production lines: can edible oil and bottled water be filled using the same machine? The short answer is — technically yes, but it’s not recommended without significant customization. In this article, we’ll explore the key technical differences between the two products, what it takes to adapt a filling machine for both, and when it makes sense to separate your production lines.
This article was inspired by a recent inquiry from one of our clients in Bangladesh, who asked whether they could run both bottled water and edible oil on a single filling line. Their primary challenge? Cleaning between product changeovers — a problem that resonates with many producers in developing markets. We invite others with similar experiences or questions to join the discussion.
Key Differences Between Edible Oil and Bottled Water
Before deciding whether an oil filling machine can be used to fill water, it’s essential to understand the fundamental physical and operational differences between the two products. These differences directly impact equipment compatibility, accuracy, and hygiene management.
Viscosity and Flow Behavior
Oil is generally much more viscous than water. Most oil filling machines are designed with pumps, valves, and pipelines that accommodate slower, thicker flow. When used to fill water — which flows much faster — these systems may overfill, underfill, or splash due to the mismatch in fluid dynamics. Without parameter adjustments, such as slowing down the filling speed or reducing pump pressure, accurate filling becomes difficult.
Foaming and Splashing
Bottled water may foam slightly at high-speed filling, which can be controlled with specialized nozzles. Edible oil does not foam, but its slower flow requires longer filling times and precise control to avoid dripping or underfilling.
Temperature Sensitivity
Some edible oils need to be filled at elevated temperatures (e.g., palm oil), while water is usually filled at ambient or even chilled temperatures. Sharing a filling system would require wide temperature tolerance in pumps, valves, and pipelines.
Hygiene and Cross-Contamination
If a machine has previously been used to fill edible oil, its internal surfaces — especially in the pipelines and valves — may retain oil residues. This presents a significant hygiene risk when switching to bottled water, particularly in the food and pharmaceutical industries. Residual oil can impact water clarity, taste, and safety. Thorough and validated cleaning protocols (CIP or manual) are essential before switching products.
Filling Valve Considerations
Water filling typically uses gravity or pressure-based valves designed for high speed and low-viscosity liquids. Edible oils require piston fillers or flowmeter-controlled valves that can handle thick, slow-moving liquids.
Industry Insight: In our experience, companies that attempt to use a one-size-fits-all valve often face frequent maintenance issues, inaccurate fills, and eventual redesigns. A customized filling valve is essential for dual-use.
Material Compatibility
Water can be filled with standard 304 stainless steel construction. Edible oil, especially those with high acidity, may require 316L stainless steel or food-grade seals (e.g., FKM or PTFE) that resist swelling and degradation.
Gaskets and seals that work well for oil may deteriorate faster when exposed to aggressive water-based cleaning agents, creating long-term maintenance issues.
Changeover Time and Cleaning Complexity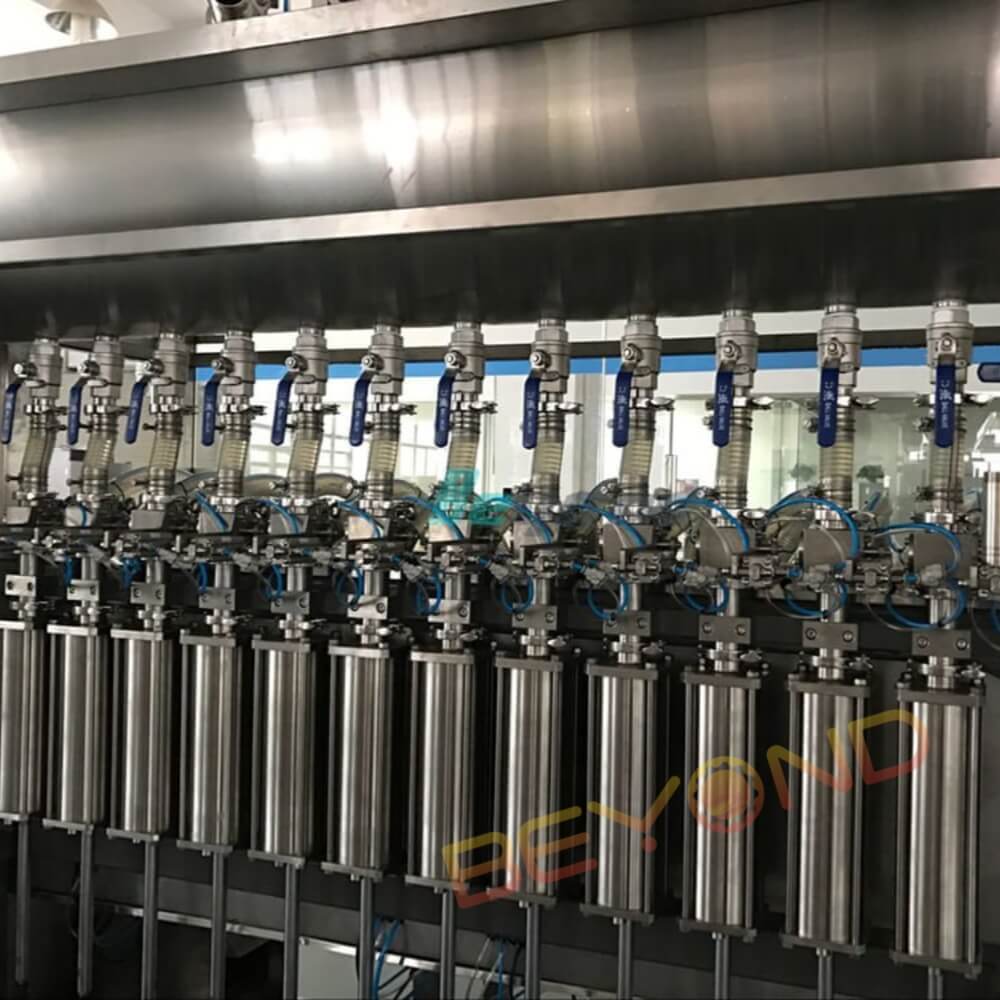
Switching between edible oil and water requires complete disassembly or a robust Clean-in-Place (CIP) system. Oil residues cling to tanks and pipelines, making cleaning time-consuming. Water demands a clean, odor-free environment. These operational frictions reduce Overall Equipment Effectiveness (OEE).
In our client’s case from Bangladesh, cleaning was the most difficult bottleneck — particularly removing oil film from piping and valves before running bottled water. While both our client and their partner engineers believe a piston-type filling machine can technically handle water — and we agree from a mechanical perspective — our primary concern remains the thoroughness of cleaning between product changeovers.
Piston fillers, by nature, have more internal surfaces and crevices where oil residue can accumulate. Even trace amounts of oil may degrade the clarity or taste of the bottled water, especially if the water is not carbonated and is expected to meet high-purity standards. This becomes a serious issue in applications where hygiene is paramount, such as premium drinking water brands or pharmaceutical-grade water bottling.
In summary, while the equipment can be shared in theory, the real-world risk lies in the residual oil impacting water quality and consumer perception. This concern is especially critical for brands with high hygiene and taste standards.
Can One Machine Handle Both with Modifications?
Yes, but only under specific conditions:
- Modular or interchangeable filling valves
- Separate product tanks and piping
- Recipe-controlled filling parameters (temperature, speed, dosing)
- Automated CIP systems
These features increase initial investment but allow for flexible, multi-product use.
Expert Tip: We’ve seen success with high-end flowmeter fillers that use magnetic or mass flow measurement, allowing precise filling of both thin and thick liquids without changing valves — but these machines come at a premium.
Alternative Recommendation
If your production volumes are high, consider investing in dedicated filling lines. This eliminates cross-contamination risk and maximizes uptime. If your budget is tight or production runs are short, opt for a hybrid system but plan for longer changeover times and additional maintenance.
Conclusion
While it is possible to fill both edible oil and bottled water on the same machine, it requires careful planning, proper design, and an understanding of the technical challenges involved. Evaluate your production needs, product properties, and long-term goals before making a decision.
Need help selecting or customizing a filling machine for multiple liquid products? Contact our engineering team for a free consultation and layout proposal tailored to your unique requirements.
We welcome all feedback and experiences — especially from manufacturers facing similar dual-product challenges. Let’s solve this together.