Beer Pasteurization Tunnel | Industrial Tunnel Pasteurizer for Bottled & Canned Beer
A beer pasteurization tunnel is an inline thermal processing machine that heats and cools filled beer bottles or cans to eliminate harmful microorganisms. It ensures product safety and extends shelf life without compromising flavor. Commonly used in medium to large-scale breweries, it offers controlled temperature zones and water spray systems.
Specifications
Parameter | Specification |
---|---|
Capacity | 3,000–30,000 bottles/hour |
Bottle/Can Diameter | 55–76 mm |
Temperature Range | 25°C–65°C |
Heating Medium | Hot water (plate exchanger or steam boiler-fed) |
Number of Zones | 5 to 11 (customizable) |
Conveyor Material | SUS304 Stainless Steel |
Control System | Siemens PLC + 10” HMI |
Power Supply | 380V, 50Hz, 3 Phase (customizable) |
Video
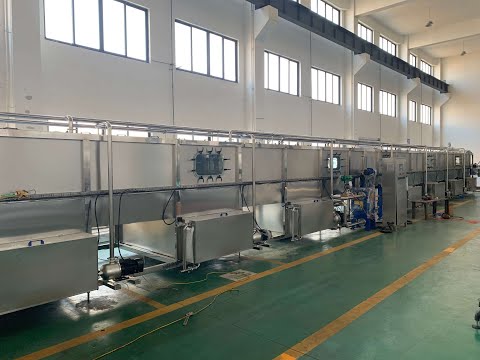
Description
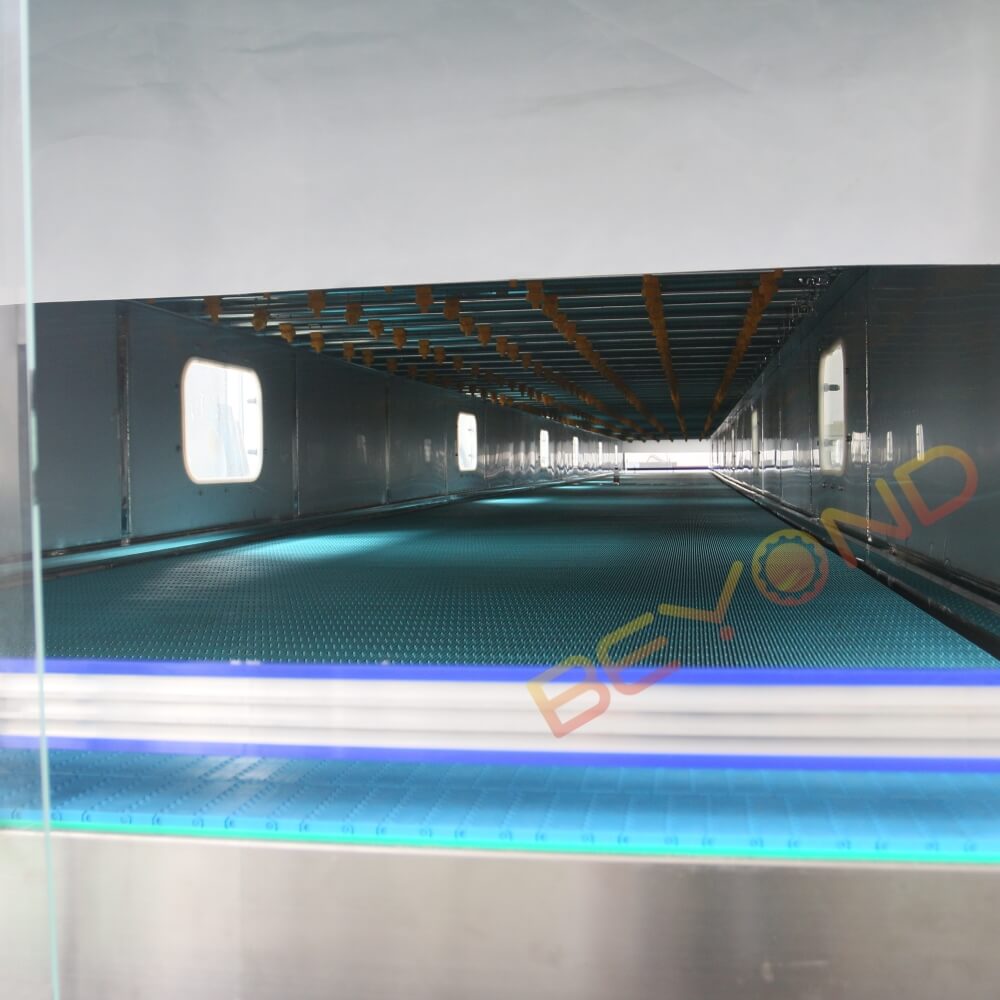
Adjustable Conveyor Speed
-
Chain plate conveyor (modular belt or stainless steel chain) supports VFD (Variable Frequency Drive) control.
-
Speed can be dynamically adjusted via HMI to match upstream/downstream equipment or adjust PU exposure time.
-
Conveyor load-bearing capacity: up to 40 kg/m²
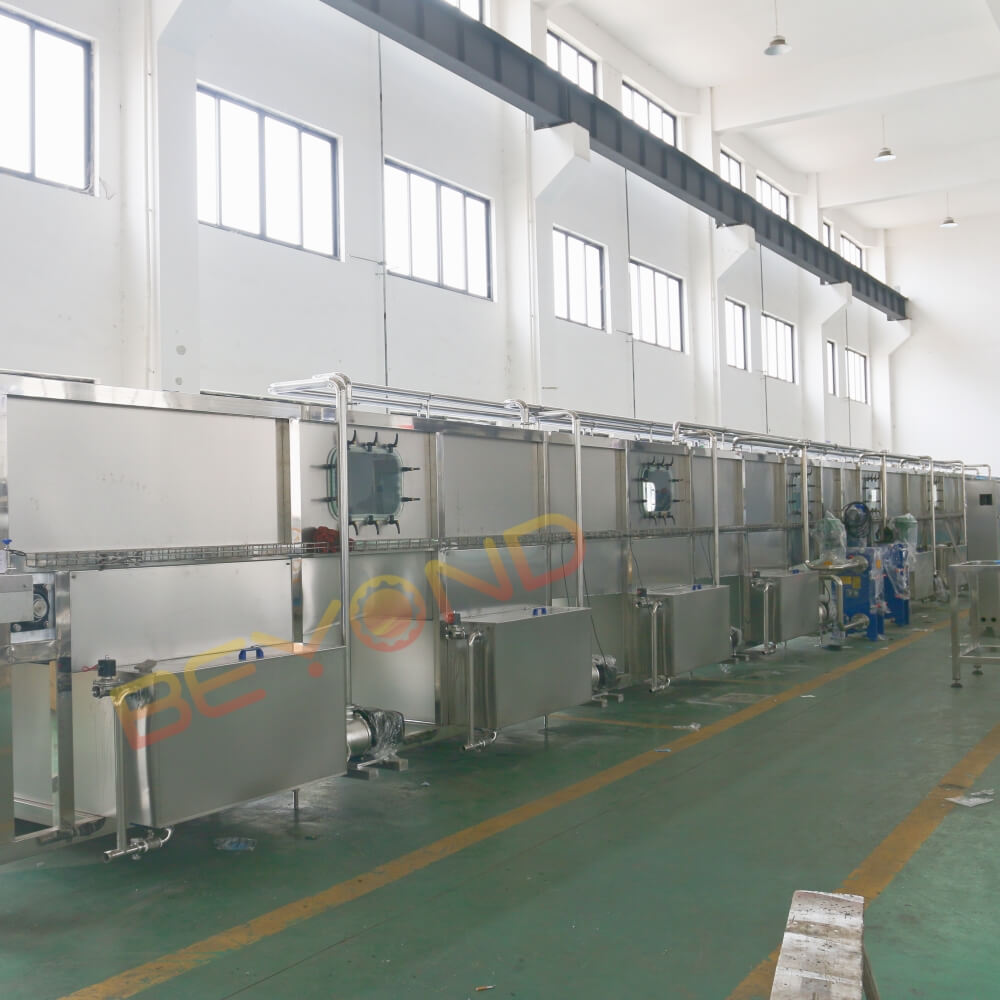
Multi-Zone Pasteurization Layout
8-Temperature Zone Control (Customized, Flexible & Accurate)
-
Divided into 8 independent spray zones:
-
2 Preheating Zones
-
3 Pasteurization Zones
-
3 Cooling Zones
-
-
Each zone features:
-
Dedicated water tank
-
Recirculation pump
-
Digital temperature sensor
-
Steam/hot water exchanger
-
PID temperature controller
-
PU Control & Logging
-
Real-time calculation and adjustment of Pasteurization Units (PU) based on dwell time, product type, and temperature profile.
-
Optional: Online PU logger with SD card storage & export.
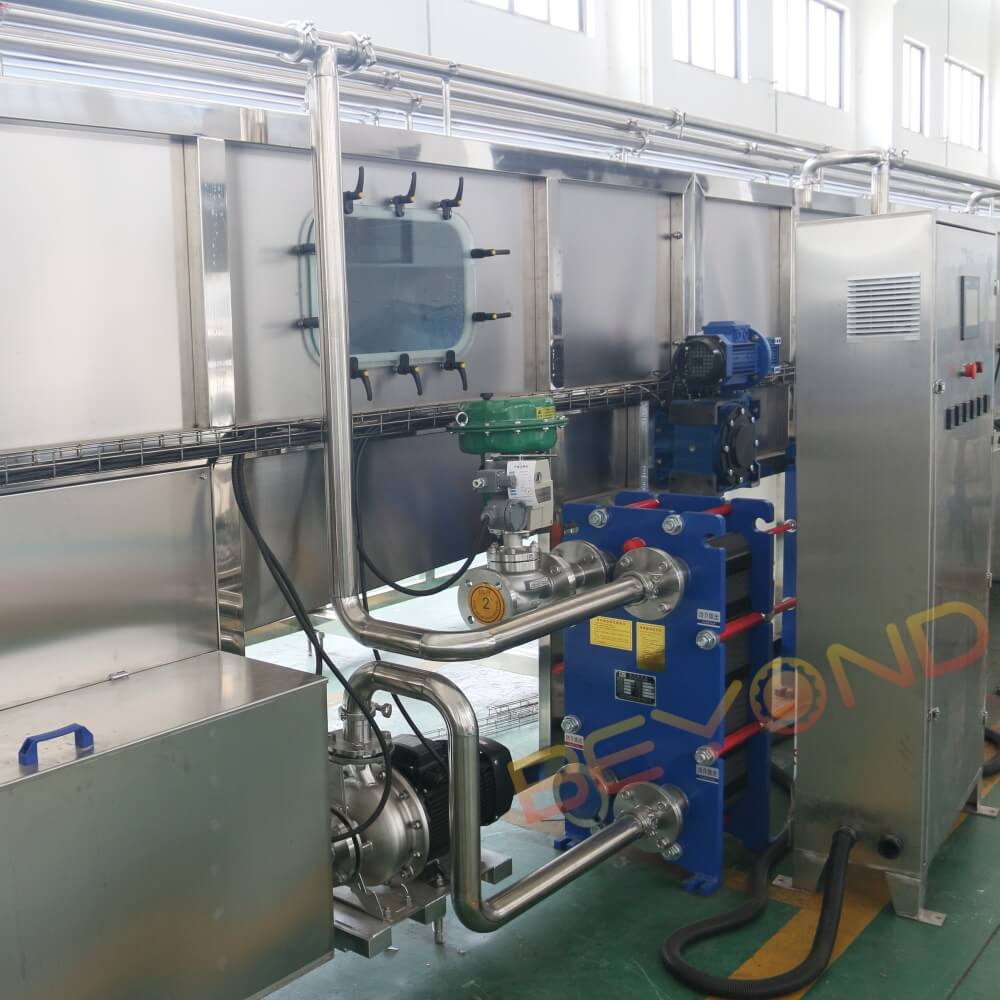
Integrated Electrical Cable Management – Side-Mounted Wire Duct Frame
To ensure safety, ease of maintenance, and professional factory layout, our pasteurization tunnel is equipped with a side-mounted cable duct frame — often referred to as a edge-aligned wire consolidation frame.
Key Advantages:
-
Neatly routes all power and signal cables along the length of the machine, avoiding cable sag or ground contact.
-
Protects wiring from heat, water spray, and mechanical interference during operation.
-
Simplifies maintenance and troubleshooting by providing clear cable paths and accessible wiring inspection points.
-
Enhances the overall appearance and hygiene of your production environment.