Ultra Clean Filling Machine |Washing-Filling-Capping | 5,000–20,000 BPH
An Ultra Clean Filling Machine is a fully enclosed washing-filling-capping system designed for sterile-grade liquid applications. It integrates ISO Class 5–7 compliant air filtration, cleanroom-level filling conditions, and CIP/SIP cleaning modules to ensure contamination-free production at speeds of 5,000–20,000 bottles per hour.
Specifications
Parameter | Value / Range |
---|---|
Output Capacity | 5,000–20,000 BPH |
Bottle Sizes | 30ml to 1000ml (customizable) |
Filling Accuracy | ±0.2% – ±0.5% |
Hygiene Classification | ISO Class 5 to 7 cleanroom-grade |
Material | SS316L (contact parts), SS304 (framework) |
Cap Types Supported | Screw, snap-on, press-fit, aluminum ROPP |
Cleaning System | Integrated CIP (standard) + optional SIP module |
Interface | Siemens PLC + 10”–15” HMI touchscreen |
Utilities Required | Sterile air, steam, RO/WFI water, power |
Description
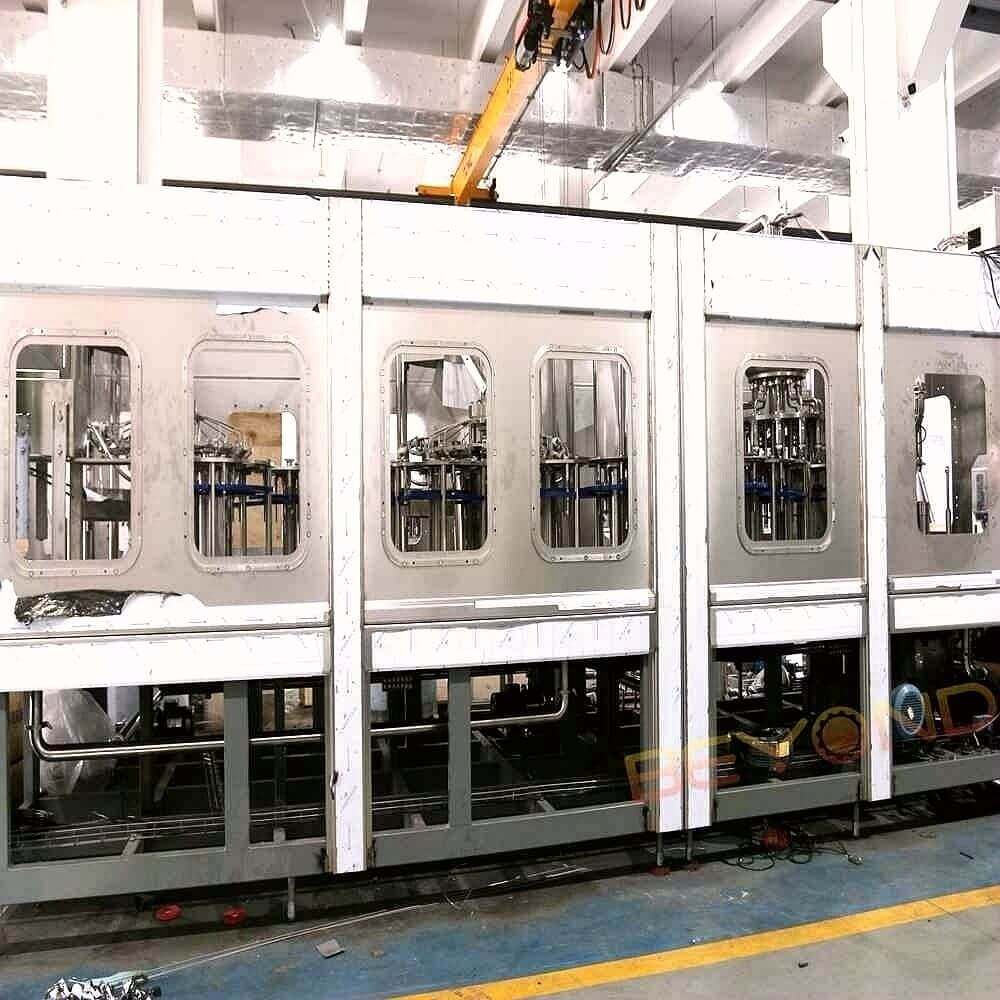
Cap Disinfection Rinse
Before being placed on the bottles, all caps undergo a targeted disinfection rinse to reduce microbial load and surface contaminants:
-
Disinfection Medium: Typically involves a diluted hydrogen peroxide (H₂O₂) or peracetic acid solution (adjustable based on product compatibility)
-
Sterile Spray Tunnel: Caps are conveyed through an enclosed spray tunnel with high-pressure nozzles positioned to ensure complete surface coverage
-
Optional Air Knife Drying: After rinsing, sterile air knives may be used for surface drying before feeding to the capping station
-
Validation Ports: Integrated sampling and drain ports enable residue and effectiveness validation per GMP protocols
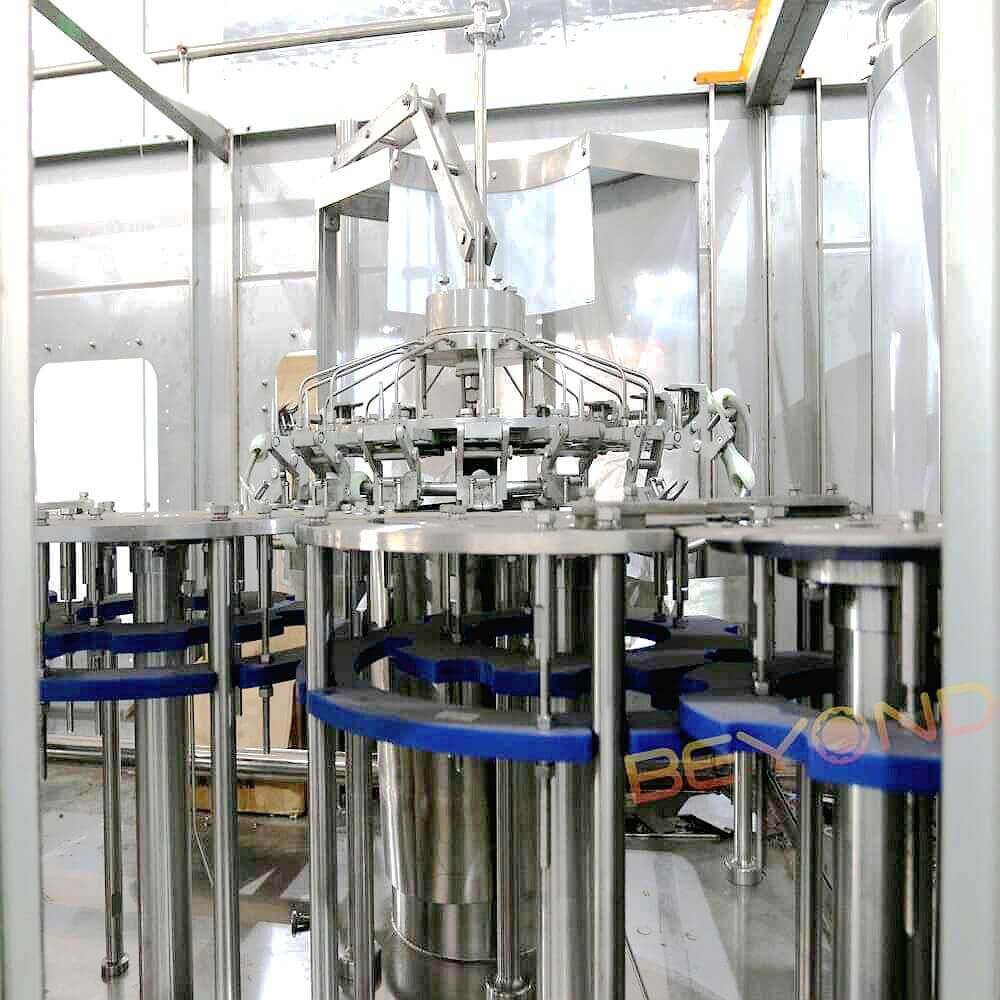
Bottle Body Disinfection Rinse
This stage ensures that all bottles are effectively disinfected on both internal and external surfaces before entering the sterile-grade filling zone:
-
Inversion Gripper Design: Bottles are held by neck grippers and rotated 180° for complete internal access
-
Chemical Rinse Medium: Adjustable concentration of disinfectant (e.g. 0.5–1% H₂O₂ or chlorine-based agents) based on contamination risk and container type
-
Multi-Nozzle Jet Spray: Strategically arranged jets clean inner walls, bottle necks, and outer surfaces simultaneously
-
Drain Control: Residual disinfectant is collected via stainless steel drainage system and diverted from clean zones
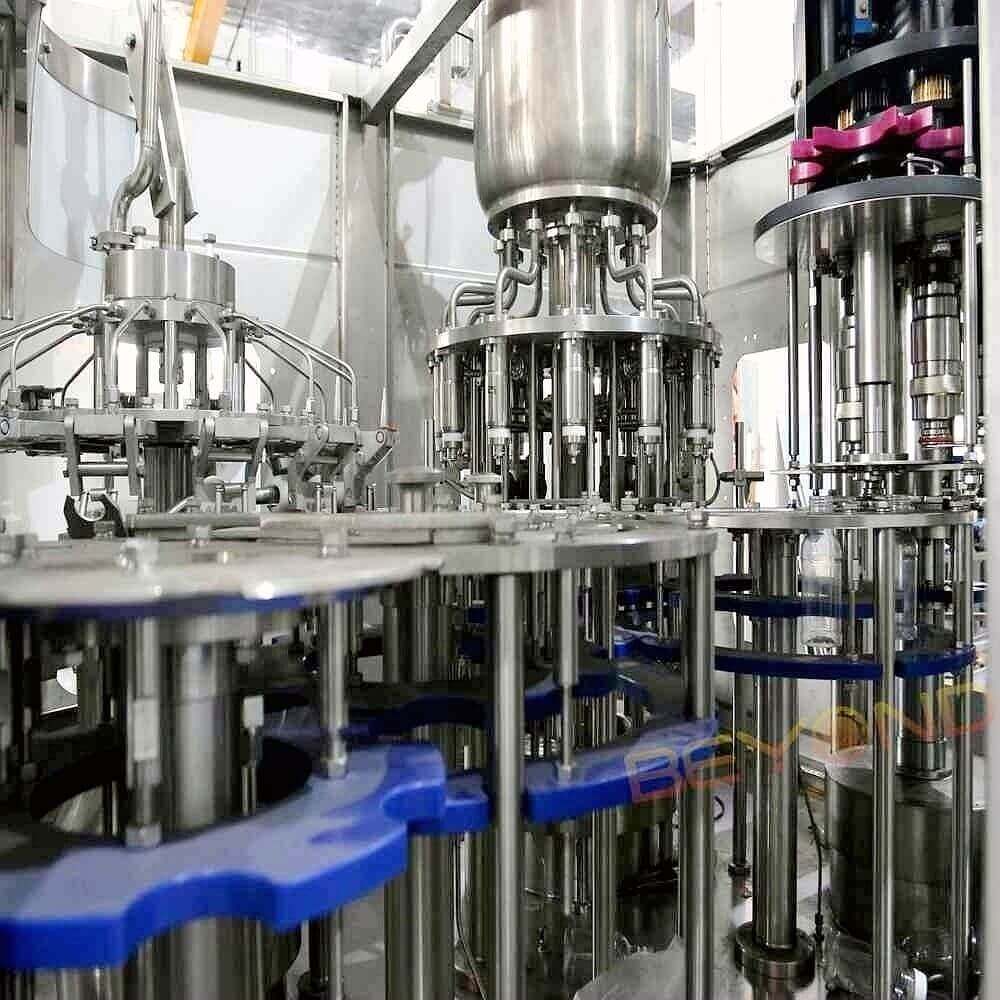
Sterile Water Rinse (Final Rinse)
After disinfection, a final rinse is performed using purified water to eliminate chemical residues and ensure product safety:
-
Water Source: USP-grade Purified Water or Water for Injection (WFI) based on application (pharma/cosmetic/food)
-
HEPA-Filtered Air Blow Option: Post-rinse air knife can be included to reduce residual water before entering filling zone
-
Enclosed Rinsing Chamber: Rinsing is carried out in a fully enclosed area with laminar flow (ISO 5–7) to maintain sterility
-
Sanitary Design: All water contact piping and nozzles are 316L stainless steel with tri-clamp connections and automatic CIP-compatible
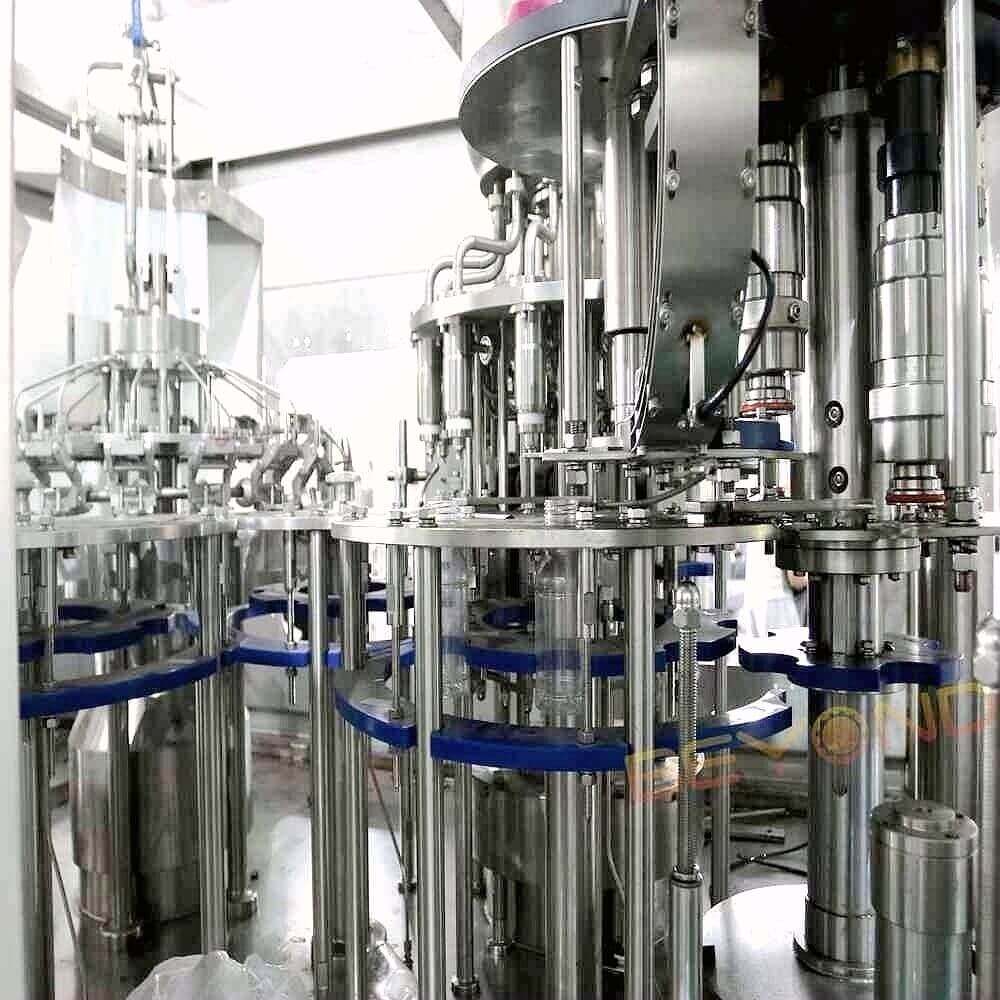
Cylinder-Lift Bottle Platform for Positive Seal Filling
During filling, each bottle is positioned precisely beneath the filling valve and then lifted upward by a pneumatic cylinder to create a tight seal between the bottle neck and the filling nozzle. This vertical motion is synchronized with valve operation to ensure a completely enclosed transfer of liquid with no splashing or foaming.
Key features:
-
Smooth High-Speed Motion: Pneumatic bottle lifts are engineered for high-speed movement with minimal vibration, ensuring reliable performance even at 20,000 BPH.
-
Secure Bottle-Valve Seal: The bottle neck contacts the valve nozzle directly and forms a sealed interface before the valve opens, preventing airborne contamination and vapor backflow.
-
Anti-Drip Shut-Off Mechanism: Once the liquid level reaches the preset fill height, the valve closes first, then the cylinder lowers the bottle. This sequence eliminates splash-back or dripping that could contaminate the bottle rim or cap area.
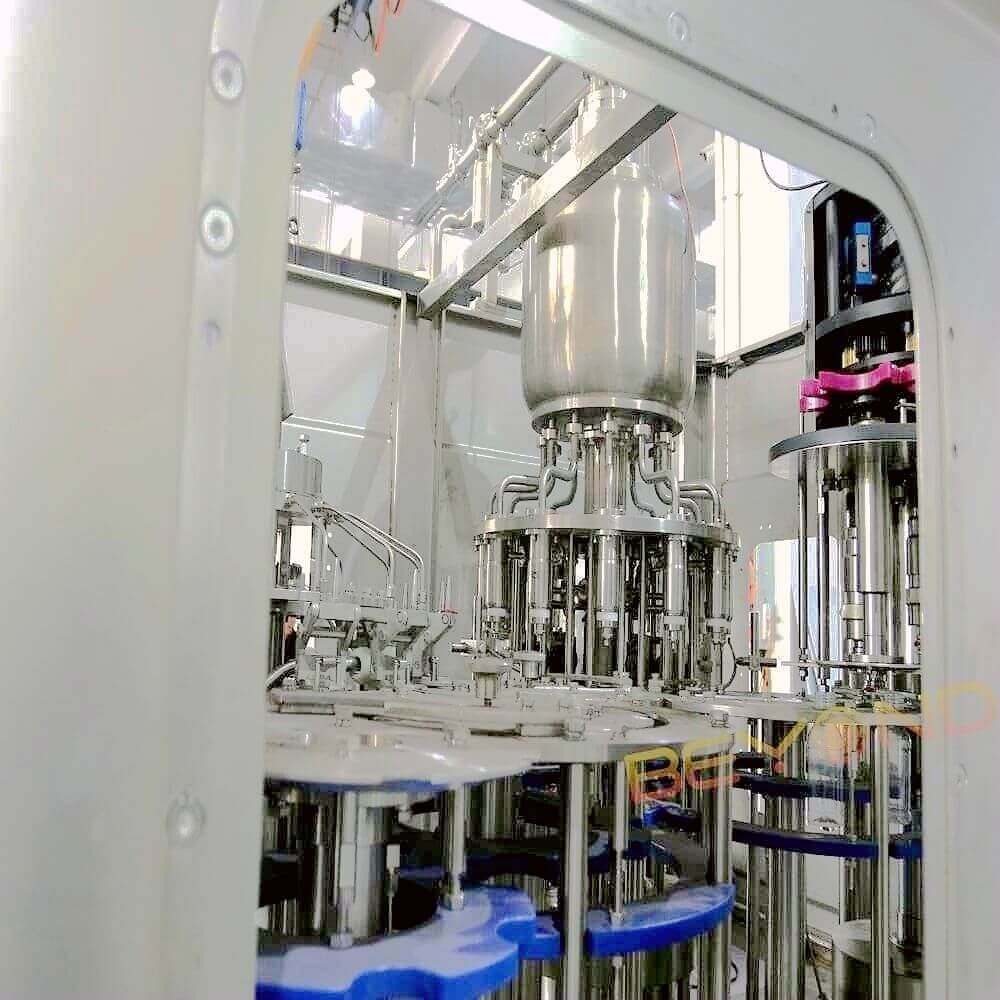
Capping Head Rotation and Sealing Process
Capping is carried out by magnetic torque capping heads that perform coordinated rotary actions under cam control. Each head simultaneously revolves and rotates, completing a multi-phase closure sequence:
-
Pick-up Mechanism: Caps are fed via chute to a rotary sorting disc; each capping head picks up a cap using a top cover shaft that stabilizes and centers the cap in the sealing mold
-
Cap Placement & Tightening: Under cam guidance, the capping head lowers, fits the cap onto the bottle, and applies constant magnetic torque to tighten it
-
Slip-Proof Closure: Once the preset torque is reached, the magnetic clutch allows the head to slip, preventing over-tightening or damage